Source Link
The Issue
Additive manufacturing (AM) is a promising technology that many AM practitioners believe is on the precipice of a breakthrough. This breakthrough would be realized when AM is incorporated into supply chains and manufacturing processes throughout the economy and when innovators use AM to re-architect existing systems and reshape entire industries. AM has been expanding in recent years, with annual growth rates averaging over 20 percent and several billion dollars annually in both parts produced and AM services provided. It has penetrated multiple industries, especially aerospace and defense, medical devices, and tooling, where it is primarily used to improve existing systems. This approach has led to impressive growth but has not generated the widespread adoption that characterizes a true breakthrough. Forty years after some of AM’s foundational technologies were patented, its prevalence in manufacturing is growing but modest. A collection of business, technical, and workforce issues explo[red in this brief have served as barriers to an AM breakthrough. These barriers have limited the pace of AM adoption, as has the scarcity of investment capital for AM developers seeking to carry methods for overcoming these barriers across the notorious development cycle “valley of death” between research and commercialization. AM developers, manufacturers, and policymakers should work to comprehensively lower these barriers and unite around identifying and achieving an AM breakthrough in mission-based applications—“moonshot”-type problems—that only AM can enable.
The Promise of Additive Manufacturing
Additive manufacturing (AM) refers to the process by which materials are deposited and joined, layer by layer, to transform a digital model into a physical component.1 In this way, AM can be envisioned as the opposite of traditional subtractive or formative manufacturing.2 For instance, in subtractive manufacturing, components start as solid blocks of material that are then machined, milled, or cut into the desired shape.3 In formative manufacturing, empty molds of a desired shape are filled with liquid and allowed to solidify.4
In contrast, AM is a digitized process wherein components are modeled using computer-aided design (CAD) tools, which machines then translate into components by depositing materials additively in the specified shape.5 The breadth of AM techniques is best understood as a collection of processes, materials, and applications. For instance, AM’s binder jetting process uses a printer head to deposit a bonding agent that joins layers of powdered sand, polymers, or metals.6 AM’s direct metal laser sintering (DMLS) process, on the other hand, fuses layers of metal powder together using a laser.7
AM has already achieved significant progress in market adoption. Initially, the AM marketplace was dominated by engineers who leveraged AM to enable rapid prototyping.8 It later received broader public notice and attention with its adoption by hobbyists who used 3-dimensional (3D) printing to create personal items of their own design. Today, however, AM capabilities are applied in the aerospace (e.g., producing rocket engine injectors), medical (e.g., producing orthopedic implants, prosthetics, and heart implants), and tool and die (e.g., constructing large parts) industries.9 AM capabilities have also been used to manufacture personal protective equipment (PPE) rapidly and flexibly during the Covid-19 pandemic.10 Altogether, the AM sector produced $11.87 billion in value in materials and services in 2019.11 Given overall U.S. manufacturing activity of $13.8 trillion in 2019, achieving an AM breakthrough would require the sector to grow by at least an order of magnitude to a scale of hundreds of billions. AM has demonstrated its ability to rapidly expand its presence in the economy through three key advantages: managing complexity, enabling mass customization, and shortening product lead times.12
First, rather than manufacturing numerous individual components and welding them into complicated configurations, AM can consolidate parts and produce complex geometries in a single, integrated process.13 By streamlining the manufacturing process and reducing the tooling required to produce and assemble many separately manufactured subcomponents, AM can reduce the cost and time required to produce complex components. Furthermore, by enabling close integration without welds and fasteners, AM can also reduce component mass. In certain applications, reduced mass may translate into increased performance; for example, by using AM to produce an aircraft engine fuel nozzle, General Electric increased engine efficiency by 15 percent.14 Other aerospace companies, including Aerojet Rocketdyne and SpaceX, are also using AM to produce rocket engine components, and a new company, Relativity Space, is working to manufacture an entire rocket using additive methods.15 In addition, AM processes generally produce less waste materials than subtractive manufacturing alternatives, and reduced part counts can also reduce costs and environmental impacts from shipping numerous subcomponents between companies for further assembly. AM processes also create new opportunities for recycling or reusing materials such as waste products, which can be turned into feed material for AM.16
Given overall U.S. manufacturing activity of $13.8 trillion in 2019, achieving an AM breakthrough would require the sector to grow by at least an order of magnitude to a scale of hundreds of billions.
Second, the highly digitized nature of AM enables “mass customization.”17 Companies can customize designs—changing their size, geometry, or other properties—using CAD software and then print multiple unique products using the same machine. For instance, nearly all major hearing aid companies use AM to produce geometrically complex hearing aids made to each user’s specifications.18 Another company, Align Technology, has adopted AM to enable “mass customization” of orthodontic devices that are tightly fit to the unique dental features of each individual.19 This approach for applying AM to quickly build highly customized products in large volumes quickly leverages the advantages of AM compared to the mass production economy of scale advantages of traditional subtractive manufacturing.
Third, AM enables companies to respond to market changes quickly by making limited changes to the materials, process, or infrastructure required to produce an item, thereby improving crisis response by shortening product lead times.20 This leverages AM’s original strength in rapid prototyping to enable rapid improvements in the production process in near real time. For example, during the Covid-19 pandemic, companies such as Hewlett-Packard and Formlabs leveraged in-house AM capabilities to produce face masks, shields, and testing swabs to meet rapidly emerging public health requirements.21 In addition to responding rapidly to changing market conditions, AM can also be used to help companies rapidly relocate and onshore the production of critical capabilities, especially those that support crisis response, and deal with unexpected supply chain disruptions. Using more efficient AM processes, companies can shorten the lead times for large parts by producing them domestically.22 For example, in an effort to reduce ship downtimes due to maintenance, the U.S. Navy is exploring opportunities to print long-lead or obsolete parts locally, perhaps even onboard ships.23
AM has leveraged these three key advantages to achieve the impressive growth rates of the last several decades. An AM breakthrough will require capitalizing on these advantages to fundamentally reshape manufacturing processes across multiple industry sectors. Successful innovation is typically the result of the combined efforts of many people. People and organizations working with varying levels of cooperation, competition, and collaboration form an innovation ecosystem—including universities, government laboratories, and private-sector companies—to overcome barriers to commercialization.24 Innovators in many industries are using AM to improve existing designs gradually rather than to re-architect systems or reshape entire industries.25 However, some have used AM to fundamentally reshape the manufacturing process in limited areas, such as space and medical devices, where the economic incentives are clearly favorable to AM.
To assess both barriers and opportunities for continued innovation, the CSIS study team conducted a literature review and interviewed 22 stakeholders from across the AM innovation ecosystem. Through this work, the study team argues that in order to achieve an AM breakthrough—wherein innovation accelerates and drives disruptive change throughout the economy—government and industry actors in the AM innovation ecosystem should work to comprehensively lower barriers to AM adoption, support the transition of solutions to these barriers across the innovation valley of death, and unite around identifying and achieving an AM breakthrough in mission-based applications—“moonshot”-type problems—that only AM can enable.
Toward a Breakthrough
Innovation, both incremental and disruptive, fuels economic growth.26 There may be no reason, therefore, to prefer disruptive innovation to incremental innovation. But incremental improvements, especially to complex manufacturing systems that rely on infrastructure-intensive tooling and processes, can take decades to effect significant change. Forty years after AM’s foundational patents were awarded, the field has largely remained in an incremental innovation paradigm. The barriers that AM faces constrain both incremental and disruptive application of AM. Technical issues with the technology must be solved to achieve broader adoption, business model challenges limit the availability of capital for carrying solutions across the development valley of death, and workforce challenges slow AM adoption. Facilitating an AM breakthrough by addressing these barriers is a non-trivial endeavor—one that requires sustained efforts by both public- and private-sector actors. Undertaking this endeavor will benefit AM adoption under both innovation paradigms.
There are reasons, however, to believe that more disruptive forms of AM adoption are primed to advance because developments in related technologies and economic shifts have the potential to support and reinforce an AM breakthrough. For example, the digital nature of AM, as well as the automated process by which components are created, has led some scholars to identify AM as a foundational enabler of the fourth industrial revolution, or “Industry 4.0.”27 In this futuristic vision, “smart” factories integrate digital and physical systems to increase production flexibility and efficiency.28 AM, which translates digital designs into physical components, is therefore emblematic of and will be supported and reinforced by an Industry 4.0 future.
In Industry 4.0’s futurist vision, the integration of multiple capabilities—big data, cloud computing, AM, and autonomous systems—is what creates economic value.29 In other words, the Industry 4.0 vision requires new connections between capabilities (i.e., new system architectures). For this reason, it may be useful to consider AM through the lens of architectural innovation, where the dominant changes to existing systems do not occur solely within system components, but rather in those components’ interactions and linkages.30
Indeed, AM’s greatest potential lies in fundamentally reshaping the structure of existing systems. For instance, AM has already demonstrated its ability to manage complexity by combining disparate components into single, integrated structures; almost by definition, changing linkages between components—as well as managing complexity among them—requires architectural change.31 And although AM-induced architectural changes are currently present in subsystems and components, today’s capabilities illustrate the potential for system-wide architectural innovation in the future.
For example, innovators could re-architect today’s systems using AM to enable continuous operation in remote or austere locations, such as offshore oil rigs, by allowing the production of key spare parts and supplies directly at these locations, diversifying the manufacturing of replacement parts.32 Similarly, innovators could use AM to forge new connections between nodes in key global supply chains. By redesigning parts to enable shorter, less complex supply chains where leveraging economies of scale is less critical, AM can be an enabler of onshoring the production of critical capabilities that have previously migrated offshore. Further, by enabling the rapid stand-up of production facilities which can produce new or newly modified products in quick response to changing market conditions, AM can enhance the ability of supply chains to react to demand. This aspect of an AM breakthrough is likely to be particularly relevant in supply chains where AM advantages such as mass customization and responsiveness are critical. This effect was demonstrated by the use of AM to onshore the production of various products, including medical equipment, during the Covid-19 crisis.33 In these examples, AM’s potential derives from its ability to reconfigure the interactions and interdependencies among complex system components.
An Innovation Trajectory Full of Barriers
Innovation is often envisioned as a linear, incremental trajectory.34 The trajectory starts with basic science, which in the case of AM may include fundamental research into material properties and machine processes.35 The process continues with invention, which proves a concept’s viability (e.g., the ability to construct a 3D component through AM processes), and concludes with commercialization.36 During commercialization, new products are developed, produced, and marketed.37
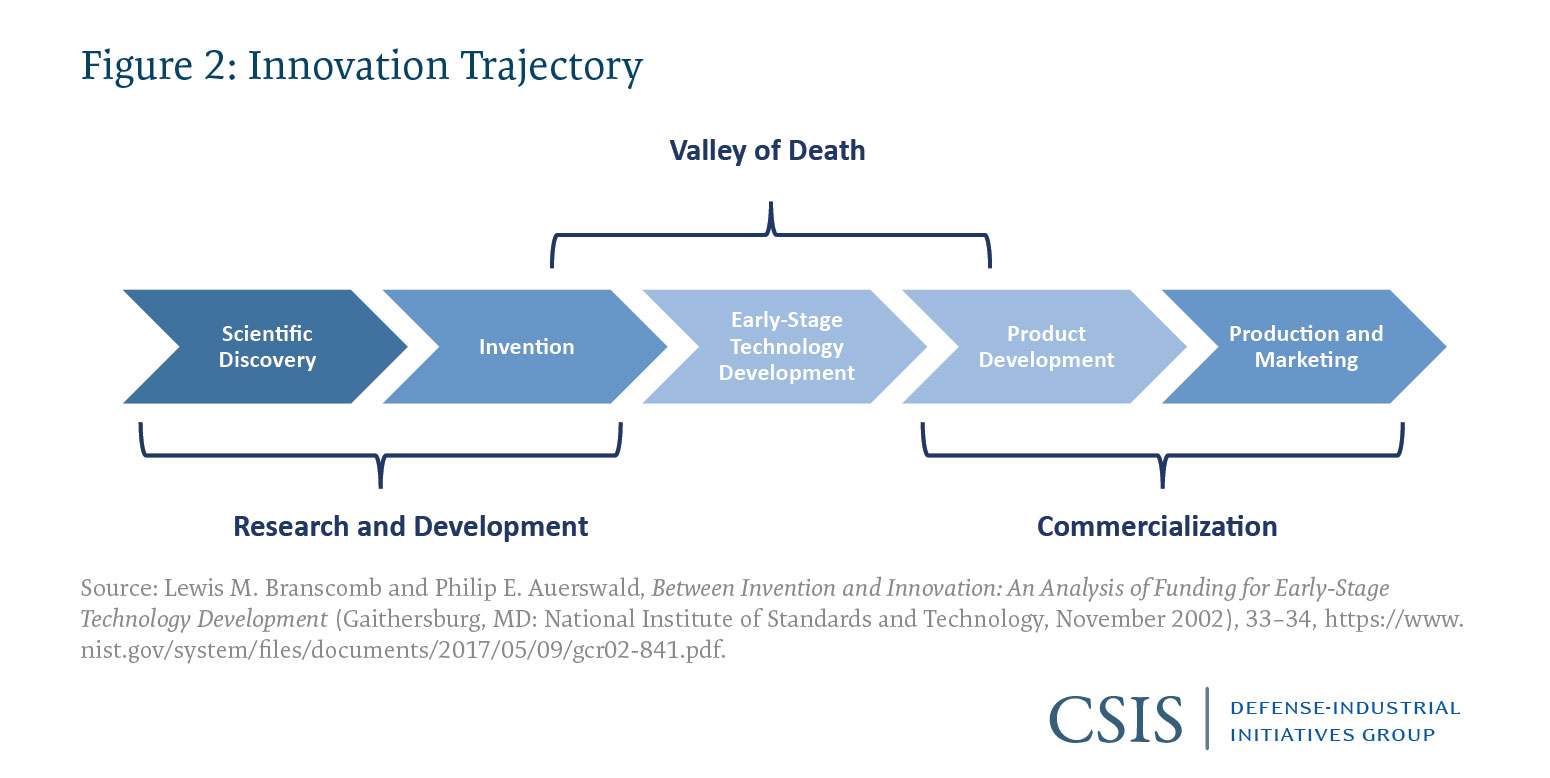
Between invention and commercialization, technologies encounter the valley of death, wherein the development cost, and therefore the capital required, to prepare a technology for commercialization increases rapidly but the uncertainty of success often overwhelms the business case for investment. True to its name, many worthwhile innovations perish in the valley of death, never to be commercialized.38 Further exacerbating the challenge posed by the valley of death is the fact that numerous trips across it are often required; indeed, innovation is rarely as simple or linear as the trajectory described above.39 AM has been no more or less subject to valley of death challenges than other technologies. However, the valley of death is a significant constraint on the availability of capital for commercializing solutions to core technical issues with AM that serve as barriers to AM adoption. A shortage of capital for solving key technical issues has been a key pacing element for AM adoption.
Like many other technologies, AM has followed a decades-long, nonlinear innovation trajectory. AM’s roots can be traced back to advancements in the late 1800s in the fields of photo sculpture and topography.40 However, despite these early scientific discoveries, one of the earliest foundational patents in AM, for Charles Hull’s stereolithography machine, was not awarded until 1986.41 Hull subsequently commercialized his invention by founding 3D Systems Corporation, which later acquired other patents, such as one awarded in 1989 for a selective laser sintering machine.42
Building off foundational work by Hull and others in the late 1980s, AM’s innovation trajectory accelerated. For example, the Institute for Defense Analyses found that between 1975 and 2011, over 3,000 AM-related patents were awarded.43 Commercialization further increased in the 2010s after initial patents began to expire and the cost of AM machines decreased.44 For instance, a new, service-based business model (i.e., “do-it-yourself” 3D printing) emerged, allowing customers to print personal items such as jewelry.45 The public’s familiarity with AM further increased when former president Barack Obama mentioned it in his State of the Union speech in 2013 and when a 3D printer was launched to the International Space Station in 2014.46 In 2019, the annual sale of AM materials and services increased to $11.87 billion, a 20 percent increase over the previous year.47 Notably, this sizable figure excludes government and private-industry investments in AM development, which fuel continued innovation.48
Today, AM as a discipline simultaneously exists at multiple points along the innovation trajectory. Some applications have been commercialized. Others require additional investments in basic science, invention, and early-stage technology development. To accelerate commercialization, innovators must navigate barriers at each juncture, obtain investment capital to develop technology to manufacturing-ready maturity, address issues of manufacturing quality and insufficient AM infrastructure, and develop new workforce skills.
Improving Manufacturing Quality
Before integrating AM components into existing systems, most organizations must first verify that they meet established quality standards. Unfortunately, compared to traditional manufacturing methods, which have undergone decades of development, the material properties of AM components remain an open area of research.49
To accelerate commercialization, innovators must navigate barriers at each juncture, obtain investment capital to develop technology to manufacturing-ready maturity, address issues of manufacturing quality and insufficient AM infrastructure, and develop new workforce skills.
For instance, as layers of material are deposited, they create a microstructure that can significantly influence components’ mechanical properties, such as hardness.50 Any uncertainty associated with these properties can induce risks within existing systems, especially in safety-critical applications in the aerospace and medical industries.51 At the same time, the high cost of systems in safety-critical applications make them good candidates for the introduction of AM since they can absorb start-up and transition costs for new manufacturing processes more readily.
In many respects, materials science is fundamental to AM. To avoid potential flaws in AM-produced materials, manual post-processing is often needed, a step that adds time and money to the production process.52 To minimize this requirement, there must be improvements in manufacturing quality delivered by the AM production process—which, depending on the application, may necessitate advancements in understanding materials science itself.53 Therefore, even as AM has already been commercialized in many applications, expanding AM still requires further investments in scientific discovery for AM materials.
Because variable material properties can induce uncertainties in the AM process itself, new inventions to improve AM production processes may also be necessary.54 Furthermore, even when material properties are well understood and consistent, the processes themselves can vary across machines, conditions, and facilities.55 The repeatability and reliability of these processes, therefore, remains a persistent barrier to more widespread adoption of AM capabilities.56 Importantly, process improvements not only require new engineering but also an advanced understanding of the basic science that governs material behaviors during the manufacturing process.57
Overcoming this barrier may require the engineers who design AM machines to adopt new closed-loop feedback control approaches; however, only a small percentage of machines currently use these more effective approaches.58 Closed-loop systems can employ sensors to detect material variations, as well as the emerging microstructure of each component. Armed with this data, machines can adjust their processes to standardize the quality of each component more effectively.
After quality improves, but before AM components are integrated into existing systems, many organizations will still require components to be certified against established quality standards. Those standards, in turn, must themselves be developed and applied to the materials and processes that are unique to AM. Additionally, new compliance procedures, such as testing and analysis, are necessary to prove that AM components can be safely integrated into existing systems.
Without standardized quality requirements or compliance processes, companies—especially those operating in highly regulated industries—face barriers to product development, production, and marketing.59 In addition to the advancements in materials science and process control described above, companies must undertake substantial testing, demonstration, and data collection to qualify AM-produced components for use.60 Essential to obtaining investment capital for these efforts is having a business case that supports them. In many cases, the business case can be justified, especially in industries where AM is flourishing, but it serves as a limiting function in the expansion and development of AM into new production processes and industry sectors. This impediment to investment is particularly challenging where AM production lines have not previously been developed or demand for AM-produced products is low, a classic challenge for those seeking to cross the valley of death. Absent internal time and money to invest in these activities, companies must rely on publicly available standards—many of which remain a work in progress but hold promise for helping to mitigate some of these challenges.
Enhancing Manufacturing Infrastructure
The infrastructure required to accelerate adoption and to scale AM’s deployment across the economy also remains a work in progress.61 The envisioned Industry 4.0 infrastructure consists of a digital–physical architecture that integrates sensors, big data analytics, automation, and AM.62 To achieve that vision, there must be continued innovation in the architecture’s enabling components, such as artificial intelligence (AI) and automation. For AM specifically, its architecture’s digital nature also necessitates substantial changes to computing (both hardware and software), cybersecurity, business interests (e.g., intellectual property protection), and the workforce infrastructure that has traditionally supported manufacturing.
For example, further work is required to integrate and adopt software design tools for AM machines and to enhance those machines by integrating software-intensive components such as advanced sensing capabilities, AI-enabled data analytics, and closed-loop feedback control. Today, however, those supporting software systems are often poorly integrated, creating inefficiencies in the AM process.63 The need to piece together disparate software solutions into an integrated computing infrastructure may disincentivize product developers who might prefer to buy integrated, off-the-shelf software.64
Another barrier is the need to safeguard those digital systems. For example, hackers might exploit AM systems for espionage or for profit; indeed, researchers at the Massachusetts Institute of Technology (MIT) note that AM “reduces the barrier to entry for counterfeiters.”65 More nefarious cyber actors might also seek opportunities to sabotage digital designs and cause component failures.66 Absent an enhanced security infrastructure to guard against these vulnerabilities, many organizations may remain reticent to produce and market products that rely on AM.
Companies may also hesitate to produce and market AM-enabled products because they require changes to the surrounding business landscape. For instance, intellectual property (IP) protection is more complicated for AM than for traditional methods and may involve protections for everything from digital designs to software, materials, machines, and printing processes.67 Researchers at MIT predict that AM is likely to induce “a fundamental shift” in the patenting process.68 Such shifts, in turn, are likely to affect companies’ business models and how they award contracts—changes that might initially deter some companies from adopting AM more broadly.
Finally, to overcome barriers at all phases of the innovation trajectory, the innovation ecosystem requires a strong, interdisciplinary workforce. That workforce needs to not only understand the basic principles of manufacturing but also AM-specific materials science and processes.69 Furthermore, the digital nature of AM creates requirements for new digital design skills; for example, design for additive manufacturing (DfAM) is a new approach that enables engineers to consider key AM variables (e.g., component quality, geometry, and production process) when developing digital designs.70 Therefore, unlike traditional manufacturing methods, innovation in AM requires a workforce that is fluent in both digital and physical systems, as well as in their integration.
Availability of Investment Capital
Within the innovation ecosystem, numerous public- and private-sector actors are working hard to address the barriers described above. Their work, however, often focuses primarily on research and development (R&D) and commercialization. Capital available for developing technology to a manufacturing-ready level of maturity—the phase that houses the valley of death to which so many promising technologies succumb—is limited.71 As long as few actors invest near the valley of death, an AM breakthrough will remain distant and the potential for AM to revitalize manufacturing in the United States will be limited.
R&D INVESTMENTS
Public- and private-sector actors can address barriers early in the innovation trajectory by investing in R&D. For AM, private-sector R&D is particularly robust; for instance, two of the four foundational AM patents were developed by industry without government funding.72 Additionally, corporations received 75 percent of the more than 3,000 AM-related patents issued from 1975 to 2011.73
Complementing industry’s foundational role, government agencies promote R&D investment and facilitate collaboration across the private and public sectors. Government agencies fund research grants at universities, nonprofit organizations, and companies. Indeed, despite the private sector’s foundational role in AM R&D, it is worth noting that projects funded by the National Science Foundation (NSF) shepherded the development of three prominent, commercialized AM processes: binder jetting, powder bed fusion, and sheet lamination.74 Furthermore, as of 2013, the NSF had awarded almost 600 research grants for AM-related projects.75
Government agencies also provide support to businesses for AM-related technology development. The NSF, for instance, supports private-sector research through the Small Business Innovation Research (SBIR) program, through which it awards $200 million in funding each year.76 Other government agencies, including the National Aeronautics and Space Administration (NASA), the Department of Energy (DOE), and the Department of Defense (DOD), also provide direct support to small business R&D.77 For the government agencies investing in AM, SBIR has been a key resource. However, the bulk of SBIR funding goes for Phase I and Phase II SBIR grants which support concept development and feasibility-related work. The more challenging, valley of death–related work that bridges from R&D to commercialization, known as SBIR Phase III, cannot be funded from SBIR funds and has little to no dedicated funding elsewhere in agency budgets.78
Government agencies also promote R&D through public-private partnerships. The DOE’s Oak Ridge National Laboratory (ORNL), for example, houses a 110,000-square-foot manufacturing demonstration facility, the state-of-the-art capabilities of which are available to private sector, university, and government researchers.79 ORNL operates under a cooperative research and development agreement (CRADA), which allows private-sector researchers to license IP that is developed using ORNL facilities, personnel, and equipment.80 ORNL’s partnership with Lincoln Electric’s Wolf Robotics, for instance, allows the company to leverage federal facilities to manufacture large-scale parts.81 The ability to pilot and demonstrate AM processes at ORNL can mitigate some of the business case uncertainties that limit the availability of investment capital in the valley of death.
Continued investment in these and other types of R&D, especially in AM barrier areas such as materials science, closed-loop feedback control, software integration, and cybersecurity, will enable the AM innovation ecosystem to shorten development cycles for new AM products and processes. Importantly, although R&D investments serve as an engine for innovation, they alone are not sufficient to enable widespread commercialization. To achieve this end, the innovation ecosystem must also overcome barriers during the later phases of the innovation trajectory.
INVESTMENTS IN COMMERCIALIZATION
As R&D improves manufacturing quality, the slow pace of development of accepted quality standards for AM processes and products, as discussed earlier, becomes a significant barrier to commercialization. Numerous actors are devoted to standards development. Dedicated organizations such as ASTM International collaborate with public- and private-sector actors to “define terminology, measure the performance of different production processes, ensure the quality of the end products, and specify procedures for the calibration of additive manufacturing machines.”82 Unlike other institutions, rather than waiting until after R&D is complete to develop standards, ASTM International engages with the public- and private-sector research communities to develop standards in parallel with R&D.83
Government agencies, including NASA, the Federal Aviation Administration (FAA), and the National Institute of Standards and Technology (NIST), support activities led by ASTM International and other standards organizations, such as the International Organization for Standardization.84 Although industry participation in defining standards is voluntary, companies may choose to opt in when it would be cost-prohibitive for them to develop proprietary standards and compliance methods and where the benefits are greatest when a standard is widely adopted. However, some companies may view internal standards and compliance methods as a competitive advantage that should not be shared. This is often the case in areas where new processes are being pioneered or new markets developed and the number of companies likely to benefit is initially small. It is precisely the more disruptive, potentially groundbreaking types of AM development, however, where the incentive to depart from industry-wide standard development may be strongest in the short run.
Additionally, some firms may find that the infrastructure required to commercialize AM—including its associated software-design tools, digital safeguards, IP protections, and workforce—are cost-prohibitive as well. And while larger companies may have more financial flexibility to invest in such infrastructure, smaller firms may find themselves priced out of the additive market. Public-private partnerships, such as NIST’s Manufacturing Extension Partnerships, may offer smaller firms some relief in this regard.85 Public support for AM-related education—which can provide targeted, AM-specific training in topics such as cybersecurity—can also help established firms, both large and small, overcome workforce-related barriers.86
By this logic, however, new firms—unencumbered by fixed infrastructure or established workforces—may be best situated to overcome commercialization barriers. It is perhaps for this reason that AM’s innovation ecosystem includes a healthy start-up community; in 2020, venture capitalists invested over $600 million across 45 AM start-ups.87 This figure has increased since 2013, when only $100 million in venture capital funds went toward AM.88
However, private venture capital tends to fund improvements to existing products that require only a few years of investment before hitting the market.89 Indeed, venture capitalists’ focus on near-term gains often conflicts with the decades-long development timelines that are required for infrastructure-intensive technologies such as AM.90 As a result, even when an innovation ecosystem contains a healthy start-up community, barriers to commercialization may persist.91
INVESTING IN TECHNOLOGY MATURATION
Although many public- and private-sector actors are investing in R&D and commercialization, significant barriers remain to investing in the maturation of AM advances to the high state of manufacturing readiness required for crossing the valley of death, especially for technologies most essential to an AM breakthrough.92 Government R&D support during this phase is extremely limited, and VC investors are often incentivized to seek short-term return on investment timelines that favor incremental innovation over more disruptive advances where the time and cost required are substantial and risky. Frequently, neither large, established firms nor venture-backed start-ups have the incentives or ability to invest in this type of work.93 As a result, across the innovation ecosystem, few private-sector actors focus on the kind of sweeping innovation needed for Industry 4.0, where AM’s transformative potential is most likely to be unleashed.
In the public sector, a few organizations—especially the DOD-funded National Additive Manufacturing Innovation Institute, known as America Makes—do take a more holistic view of the innovation trajectory. Created in 2012, America Makes is a national public-private partnership with over 225 members from industry, government, and academia and $100 million in funding.94 Its mission is to “convene, coordinate, and catalyze” by providing connective tissue for all phases of the innovation trajectory and actors in the innovation ecosystem.95 These links proved especially valuable during Covid-19, when America Makes helped mobilize the innovation ecosystem to produce and deliver PPE across the United States.96 The Department of Veterans Affairs, National Institutes of Health, and America Makes worked together to create and validate a digital repository of blueprints for PPE that could be rapidly 3D-printed to support healthcare providers around the United States, and around the world.97
America Makes and other government organizations also develop technology roadmaps to diagnose persistent commercialization barriers, identify investment opportunities, and coordinate initiatives across the ecosystem.98 What these roadmaps lack, however, is a well-funded and executable plan to incentivize actors throughout the innovation ecosystem to bridge the valley of death.99 In particular, although these roadmaps consider AM’s application in current markets and ability to improve existing systems incrementally, they are largely silent on the strategic questions of how AM can actually achieve a systemic breakthrough.
Importantly, AM is not the only emerging capability to face this predicament. In The Entrepreneurial State, Mariana Mazzucato notes that policymakers increasingly view the government as a “facilitator” for innovation rather than as an “engine” driving it.100 Absent an explicit demand signal from a proactive public sector, however, the private sector may not be inclined to bridge the valley of death or pursue non-incremental innovation.101 Mazzucato argues that to achieve a breakthrough the public sector should assume a more proactive role.102
Achieving an AM Breakthrough
While many barriers exist that limit the pace of AM development, there are also a wide range of efforts underway to mitigate and overcome these barriers. The potential for a true AM breakthrough, however, depends on solving a range of thorny quality, infrastructure, investment, and workforce issues that span across industry and that have historically stymied individual private-sector actors and government agencies. Solving these tough problems requires significant collaboration among a wide range of private-sector actors, with active support from government. Incentivizing the investment and coordinating the sustained development activity required to achieve the AM breakthrough likely requires the public and private sectors to work together to establish a direction for AM’s innovation trajectory and an AM technology development platform to sustain support for activities that occur throughout the trajectory.103 Identifying mission-oriented applications that only AM can enable offers one strategy for setting this direction.
Mazzucato suggests that mission-oriented public policies can provide the glue that is necessary to both connect actors across the innovation ecosystem and bridge the valley of death.104 Two examples of mission-oriented policies include going to the moon and addressing climate change.105 The impetus to land on the moon drove the commercialization of integrated circuits and the development of new design methodologies, university courses, and spinoffs into industry.106 The objective to combat climate change has motivated some countries (e.g., Germany and China) to set clear goals and invest heavily in select technologies aimed at achieving them.107
To go further and realize a complete breakthrough instead, policymakers should identify and support mission-based applications in both government and commercial-focused markets for AM and related Industry 4.0 capabilities, requiring innovators to leverage AM’s potential to re-architect existing systems or reshape established industries.
The AM innovation ecosystem has not yet unified in the pursuit of mission-based applications that it can uniquely enable. Furthermore, no single actor is responsible for identifying, supporting, or coordinating efforts to achieve a shared purpose across the public and private sectors. Comprehensive efforts to lower barriers to AM adoption are clearly needed. But absent an external shock to the innovation ecosystem—one that gives its trajectory a direction—it seems likely that innovation will continue incrementally, with AM improving existing designs in current markets but without a more comprehensive breakthrough.
To go further and realize a complete breakthrough instead, policymakers should identify and support mission-based applications in both government and commercial-focused markets for AM and related Industry 4.0 capabilities, requiring innovators to leverage AM’s potential to re-architect existing systems or reshape established industries. The public sector should then provide sustained support for that goal, especially to actors that are working to bridge the valley of death. Thankfully, there are many mission-based problems where the advantages of AM can provide significant advantages, including distributed maintenance and logistics, supply chain security, new high-performance applications such as hypersonic systems, and the fulfillment of Industry 4.0. A key step toward achieving a breakthrough is for government and industry, working collaboratively together, to pick a set of tough problems and then harness the strength and ingenuity of the entire AM innovation ecosystem to work toward solving them.
No comments:
Post a Comment