By Justin Hodiak and Scott W. Harold
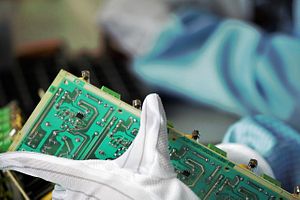
Over the past two decades, China has risen to prominence in the semiconductor industry in the areas of assembly, testing, and packaging of electronics, but it presently lags in the design and manufacture of the semiconductor integrated circuits (“chips”) which require great technological sophistication to produce. At the national level, participating in the $400 billion annual global revenue generated by the industry is a source of economic power on its own, but the industry also drives innovations in disparate sectors such as telecommunications, computing, and the automotive sector. Can China’s semiconductor industry catch up to the industry’s leading edge? How dependent is China on imported semiconductor technology today? And if it is unlikely to catch up despite spending billions of dollars, what are the obstacles it is likely to stumble on?
China has enhanced its drive to build up a domestic semiconductor capacity in recent years, most notably through its “Made in China 2025” policy together with steps more specifically targeted at the semiconductor industry, such as Guidelines to Promote National Integrated Circuit Industry, often referred to as the National Integrated Circuit Plan. Broad goals for the semiconductor sector include producing 70 percent of domestic needs within China by 2025, and reaching parity with international leading edge technology in all segments of the industry by 2030. Industrial policy for semiconductors has been an emphasis in China for more than 40 years, and these latest goals are mostly restatements of a long-standing objective to improve domestic capacity for this dual-use technology.
Knowing that China indigenously produced only 16 percent of the semiconductors it needed for domestic use in 2019, and given China’s growing efforts to reduce its dependency on foreign technology, this emphasis on increased self-sufficiency is unsurprising. However, the scale of the influx of state-backed capital into China’s semiconductor industry raised concerns about economic distortions resulting from a mercantilist policy. The funding in combination with persistent Chinese intellectual property theft elevated global concerns about how China might reach parity with leading edge design and manufacturing in this geostrategically important technology sector, particularly in light of breakthrough abilities shown in other market sectors.
In 2014, the National Integrated Circuit Plan called for investing about $150 billion in the semiconductor industry, through investments from the central government as well as provincial and municipal governments. That level of funding is equivalent to China’s annual total semiconductor market and twice what the global semiconductor industry as a whole spends annually on research and development, a substantial investment. China appears on track to reach the investment level of $150 billion in 2020 without having reached either of its stated long-term goals. And most of this investment occurred well before the United States began imposing pressure on global suppliers to cut off China’s access to advanced semiconductors. What’s holding China back?
A Technology Lag
Currently, Taiwan, South Korea, and the United States are home to the world’s leading semiconductor manufacturing facilities (called foundries or fabs, short for fabrication facility), with companies from Japan and the United States supplying the vast majority of the specialized equipment that goes into those manufacturing facilities. For its part, Taiwan Semiconductor Manufacturing Corporation (TSMC) is the world’s largest and most advanced contract manufacturer. TSMC’s high volume production is largely sustained by supplying custom chips designed by the two of the largest smartphone makers, Apple and Huawei.
Semiconductor manufacturing is capital-intensive, and the sector generally exceeds spending 15 percent of its annual revenue on research and development. Each generation of leading-edge manufacturing technology, on average, has a lifespan of only two to four years before it is overtaken by newer technology, replaced, and relegated to less lucrative products. Semiconductor manufacturing equipment vendors work in close collaboration with foundries and chip designers across international borders to maintain this relentless pace of advancing manufacturing techniques.
Today, China has no leading-edge semiconductor manufacturing facility. China’s most modern foundry only began production for creating chips from the 14 nanometer (nm) technology node in late 2019, at Semiconductor Manufacturing International Corporation (SMIC) in Shanghai. This places SMIC about a decade, and at least two generations, behind the leading edge foundries run by TSMC, Samsung (South Korea), and Intel (United States). As a reference point, TSMC has run high-volume manufacturing at the 7 nm node since 2018, and expects to have high volume production for the 5 nm node in late 2020. As a sign of their technology leadership, TSMC also has concrete plans for the following two node generations. In August 2020, TSMC publicly announced their intention to reach volume production in late 2022 for the 3 nm node, and started construction for a research center in Hsinchu for the 2 nm node. The massive investment China is making in constructing dozens of foundries primarily addresses fabricating low-end chips at older nodes, but not the nodes for highly profitable processor chips such as graphics processing units and central processing units that are used in laptops and mobile phones.
Foreign Talent Recruiting
In order to upgrade their manufacturing capability from 14 nm to more advanced, smaller nodes, China’s companies will need to develop manufacturing expertise of their own. To date, China’s companies have not demonstrated the ability to maintain collaboration networks; create and protect intellectual property; and/or maintain a workforce capable of leading edge fabrication. This stands in sharp contrast with the highly innovative assembly, testing, and packaging companies China has in this sector.
Presently, the globally-competitive talent pool for semiconductor manufacturing is limited in China. China’s manufacturing companies have aggressively recruited in recent years to lure talent away from Taiwan. Salaries at the recruiting companies in China have offered 2-2.5 times the average salaries and bonuses in Taiwan. Locations with high concentration of industry talent, such as Silicon Valley in the U.S. and Hsinchu in Taiwan, are targets that Chinese officials have identified as key priorities for poaching talent. Such locations are also centers of intellectual property theft, which often follows talent recruitment. Over the last year, more than 100 experienced engineers and managers from TSMC have transferred to foundries in China. Overall, more than 3,000 engineers are estimated to have transferred from Taiwan to mainland companies, nearly 10 percent of Taiwan’s semiconductor research and development workforce. While this recruitment rate is not a serious talent base erosion, the association with intellectual property theft warrants monitoring.
Another challenge China faces is its dependence on critical foreign technology inputs for the fabrication of semiconductors. One key type of equipment for advanced manufacturing has never been delivered to any foundry in China and therefore represents a likely bottleneck on any Chinese effort to climb the sophistication ladder to the leading edge: Namely the extreme ultraviolet (EUV) scanner that enables shrinking the integrated circuit patterning for leading edge manufacturing. Today, there is only one commercial supplier for the EUV scanners, the Dutch company ASML. In late 2019, the Dutch government did not renew an export license for ASML’s EUV scanner to be sent to SMIC in China, after aggressive encouragement from the United States. Duplicating the technologies ASML has, and that China needs, would be a substantial undertaking for China, and one not likely to succeed. ASML, its partners, and multiple national governments invested billions of dollars over more than 30 years to develop the many innovations needed for that scanner. The “fast follower” approach such as China has demonstrated in some other fields is unlikely to work in seeking to replace foreign suppliers for such complex equipment.
It is possible to manufacture at 10 nm nodes and below, possibly even down to the 3 nm node, without such an EUV scanner, through an alternative fabrication method that uses multiple overlaid patterning iterations employing older deep ultraviolet (DUV) scanner technology to achieve the pattern size reduction. The DUV scanner is equipment that has been exported to China and is unlikely to face the restrictions placed on the EUV scanner. Still, even if China’s foundries are able to use DUV scanners in fabricating chips in this way, the additional patterning will likely result in their manufacturing being more expensive overall, and with lower yield, as compared to the foundries in Taiwan, South Korea, and the U.S. that use EUV scanners.
ASML recently opened its first overseas training center with live demonstration machines in Taiwan, which has the largest installed base of its EUV scanners. ASML employs extraordinary measures to protect the intellectual property in its scanners, and placing a training center in Taiwan underscores ASML’s level of trust in collaborating there, in stark contrast to China.
Access to Leading Edge Contract Manufacturing
Increased scrutiny on exports from the United States has compounded the difficulty of accessing leading edge manufacturing for some of China’s companies. After Huawei was placed on the U.S. Entity List in May 2019. the Chinese firm needed to find alternative chip suppliers to build their smartphones. In a matter of months, Huawei switched to Taiwanese, Japanese, and Dutch chip suppliers to replace its U.S. suppliers. The extension of the U.S. restrictions in May 2020 resulted in Huawei also being cut off from having its own chip designs manufactured in Taiwan. In August 2020, Washington took further steps to prevent Huawei from circumventing U.S. export controls by shifting to foreign suppliers. The foreign-produced direct product rule was amended, and 38 additional Huawei affiliates were added to the Entity List, further restricting Huawei from obtaining foreign-made chips developed or produced with U.S. software or technology.
TSMC will stop manufacturing Huawei’s designs by September 2020 to comply with the extension of the U.S. restrictions. TSMC receives 60 percent of its revenue from the U.S. and only 20 percent from China, encouraging it to follow the U.S. restrictions rather than risk losing the larger revenue stream. In response to losing access to TSMC, Huawei increased chip manufacturing at SMIC. Domestic suppliers are not replacements for TSMC, however. Huawei explored sending designs to Samsung (South Korea) or using designs from MediaTek (Taiwan), but the August amendment of the U.S. foreign direct product rule will likely prevent this in the future. As a result, Huawei publicly stated that its shipment of smartphones in late 2020 may be the last with the new Kirin processor. More time is needed to understand if these restrictions will actually undermine Huawei through reduced mobile phone sales, or if it will be able to find alternative foreign suppliers.
Conclusion
China is presently far from its goal of self-sufficiency and global leadership across the semiconductor industry. The manufacturing segment of the industry in China lags at least two generations behind the leading edge, and depends on foreign suppliers of manufacturing equipment. The design segment of the industry is capable of globally competitive chip design, but its leading edge is reliant on foreign suppliers for manufacturing. In the short term, China is unlikely to reach parity with leading edge capabilities, and the added pressure of multiple national governments tightening export restrictions on key technologies will likely further reduce the pace of China’s semiconductor manufacturing advancement. While technology-based bottlenecks such as those highlighted here do exist, the complexity in the industry also means there are often multiple cross-border adaptations available to overcome those bottlenecks.
Decoupling and reversing supply chain integration have come to be widely discussed as policy options for dealing with U.S.-China strategic competition, yet an alternative viewpoint suggests that the better approach to dealing with interdependence and strategic competition is to rely on collective action and coordination among allies and like-minded partners to respond to shared economic and security concerns posed by China. With an actor as determined, resourceful, and dynamic as the PRC, it would be a mistake for industry analysts or national security technology policymakers to think that China’s semiconductor catch-up efforts are or will be permanently derailed. Instead, China is likely to continue pursuing multiple pathways to industrial catch-up in semiconductor manufacturing, leveraging a combination of indigenous development, foreign talent attraction programs, joint ventures, intellectual property theft, vertical integration, and other approaches identified above.
No comments:
Post a Comment