By Garrett Reim
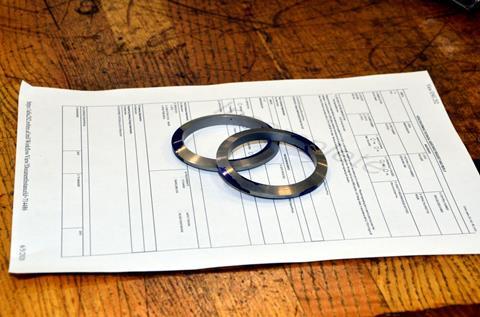
The service reverse engineered and reproduced an anti-ice gasket for the Pratt & Whitney TF33-P103, a turbofan engine which powers the Boeing E-3 Sentry, the Boeing B-52 Stratofortress and the Northrop Grumman E-8.
3-D printed anti-ice gasket for P&W TF33
The Pentagon is pushing the US military services to experiment with using 3-D printing technologies to save time and money manufacturing replacement parts for equipment, components which typically are only needed in small lots.
In August 2019, Travis AFB produced the first certified 3-D printed aircraft parts: replacement latrine covers for the Lockheed C-5M Super Galaxy.
In particular, finding replacement parts for aging aircraft can be difficult and expensive as the original part designs or manufacturers may no longer exist. Contractors sometimes charge more than the original cost of the part due to re-engineering work required. The small number of replacement components to be ordered mean engineering costs can’t be spread across a large production run, adding additional cost per part.
The anti-ice gasket project was a collaboration between the 76th Propulsion Maintenance Group, the Reverse Engineering and Critical Tooling Lab, and the Air Force Life Cycle Management Center Propulsion Sustainment Division, says Tinker AFB.
“This accomplishment is truly a historical first,” says Johnny Tsiao, Air Force Life Cycle Management Center propulsion structural competency lead. “This is a digitally designed and digitally engineered component that represents a substantial milestone in Air Force sustainment. Although it is a basic component, the technology our [Air Force Life Cycle] team has developed will help resolve supply chain issues and help bring further capacities to support the warfighter.”

Source: US Air Force
Pratt & Whitney TF33 on Boeing B-52
The service was running short of anti-ice gaskets for its TF33 and decided to try to reproduce the part in-house to save time.
“This type of engineering makes it easier to source materials, greatly reduces lead time and ultimately helps to reduce logistical and supply issues,” says Richard Banks, 76th Propulsion Maintenance Group delegated engineering authority engineer.
Using 3-D printing to create parts in house saved Tinker AFB administrative leave time, described as the amount of time between granting a contract and a component being manufactured. The service says that time period was reduced from between 120 to 136 days to 14 to 21 days.
The Reverse Engineering and Critical Tooling Lab has so far digitally engineered and printed 30 anti-ice gaskets. And, the anti-ice gasket successfully completed an engine acceptance test run, says Tinker AFB.
While the anti-ice gasket components are relatively simple, the USAF plans to try to produce progressively more complex parts in the future.
“We’ve implemented a crawl, walk and run approach when it comes to additive manufacturing,” Tsiao says. “We haven’t had a 3-D printed metal component in Air Force engines before, but in the next 12 to 24 months, this technology will open the door to more complex and critical components that help to improve our sustainment efforts moving forward.”
No comments:
Post a Comment