By SYDNEY J. FREEDBERG JR
The digital, open-architecture cockpit of the upgraded UH-60V “Victor” Black Hawk
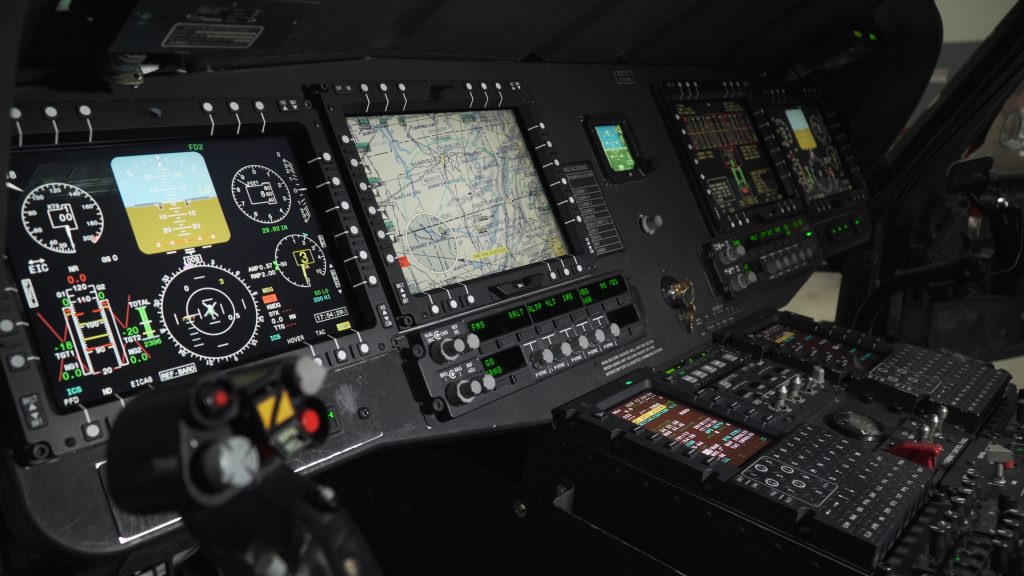
This year, the Army’s conducting five demonstrations of, in effect, prototypes for MOSA. (The mind-numbing full name is Joint Multi-Role Mission Systems Architecture Demonstration, JMR MSAD). The service has awarded at least seven contracts, three of them for what it’s calling Mission Systems Integrators, although the only competitor to publicly announce its award is Collins Aerospace (a division of United Technologies that includes the former Rockwell Collins). The MOSA demos will wrap up late next year. A proto-prototype of sorts is being developed for the UH-60V “Victor” model of the Black Hawk helicopter.
Gen. James McConville checks out the upgraded cockpit of the new UH-60V “Victor” model, which will be mainly used by the National Guard.
“We think this is absolutely critical, because we want to be able to field new capabilities very quickly into our aircraft in the future,” Gen. James McConville — the Army’s senior aviator, current vice-chief of staff, and nominee for the next chief — told the Army Aviation Association of America conference this week.
“I used to fly Kiowa Warriors,” McConville told reporters afterward. “It was a great aircraft at the time, [but] there was no open architecture…..If you wanted to change code for the multi-functional display [for example], you’d have to rewrite the entire code [for the whole aircraft] and flight test it, because…. you might impact the flight controls.”
Kiowa Warrior
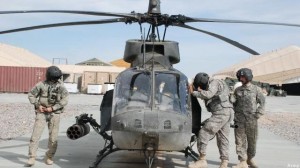
“How many people out there have mobile phones that are more than two years old?” Jeffrey White, the Army’s principal deputy assistant secretary for acquisition, asked the Quad-A conference. So why does it take multiple years just to upgrade an existing aircraft? “We’ve got to build our equipment faster. We’ve got to deliver improvements to the warfighter more quickly, we need to look … introducing upgrades over the network, much like you get upgrades to your cellphone.”
Bell V-280 Valor tiltrotor in level flight with rotors facing forward. The V-280 is widely considered the leading candidate for the Future Long-Range Assault Aircraft (FLRAA)
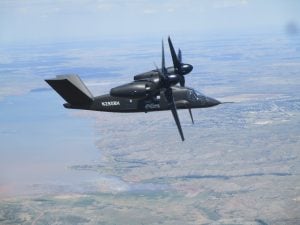
What’s more, because software and hardware were not standardized, it was often impossible to change them without knowing the original manufacturer’s trade secrets — their proprietary intellectual property. That often led to so-called “vendor lock,” when only that original manufacturer could do upgrades, with no competition on either quality or price.
The solution, much easier said than done, is to break the system into self-contained components — modules — that connect to each other like Legos using a standardized, well-defined set of interfaces — the architecture — and allow all potential competitors to know how those interfaces work — the “open” part. In theory, this allows you to take a single module of software and/or hardware made by one vendor, e.g. the cockpit displays, and replace it with a new and improved module from another vendor. Because each module is basically a black box that plugs-and-plays into the wider architecture, interacting with other modules only in strictly limited ways that everybody knows about, replacing it shouldn’t have unexpected impacts on the rest of the system and shouldn’t require learning anyone’s trade secrets to make things work together.
Sikorsky’s S-97 Raider, a leading candidate for the Future Attack Reconnaissance Aircraft, shows off its agility.
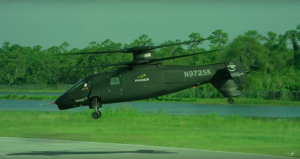
The modular approach applies most obviously to software, but has implications for hardware as well. “We don’t need a whole helicopter in order to prove out a rotor head, a landing gear assembly, or a control feature,” White said. Instead, you can just put the new component, whatever it is, on a current aircraft and see how well it works: “We can fly it, we can test it, and we can get feedback.”
Now, actually developing interface standards to allow easy plug-and-play of new components is not easy. There’s at least a foundation out there, the Future Airborne Capability Environment, which is developed and updated by a government-industry coalition, but FACE may need more refinement and detail.
Brig. Gen. Thomas Todd inspects Boeing’s AH-64 Apache production facility.
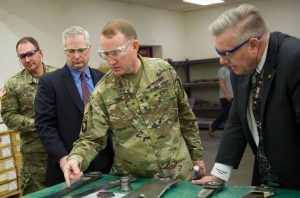
“Our first opens systems architecture cockpit is in the UH-60 Victor,” which will soon go into operational testing, said Brig. Gen. Thomas Todd, the Army’s Program Executive Officer for Aviation. “That’s really the pre-runner to MOSA. It’s helping inform MOSA as we speak.”
“We turn changes right now in that cockpit sometimes overnight, software changes,” Todd said. Instead of having to test everything every time you change anything, he said, the modules are “fully partitioned, such that this part of the aircraft doesn’t have to touch that part of the aircraft.”
“You may think that’s relatively simple,” Todd told the conference. “That’s not simple.”
No comments:
Post a Comment